Comprehensive Guide: What is Porosity in Welding and Exactly How to stop It
Wiki Article
Comprehending Porosity in Welding: Discovering Causes, Effects, and Prevention Techniques
Porosity in welding is a persistent challenge that can substantially affect the high quality and integrity of welds. As experts in the welding industry are aware, recognizing the reasons, impacts, and avoidance strategies connected to porosity is vital for accomplishing robust and reliable welds. By diving into the origin of porosity, examining its detrimental results on weld top quality, and discovering efficient avoidance methods, welders can enhance their expertise and skills to produce high-grade welds constantly. The detailed interaction of factors adding to porosity requires a thorough understanding and a positive strategy to guarantee effective welding results.Usual Reasons For Porosity
Porosity in welding is primarily brought on by a combination of elements such as contamination, incorrect protecting, and insufficient gas protection during the welding process. Contamination, in the form of dirt, oil, or corrosion on the welding surface area, develops gas pockets when warmed, leading to porosity in the weld. Inappropriate securing takes place when the securing gas, generally made use of in procedures like MIG and TIG welding, is not able to fully safeguard the molten weld swimming pool from responding with the bordering air, resulting in gas entrapment and subsequent porosity. In addition, insufficient gas protection, usually because of inaccurate circulation prices or nozzle positioning, can leave components of the weld unprotected, permitting porosity to create. These aspects collectively add to the formation of voids within the weld, damaging its stability and potentially creating structural concerns. Comprehending and attending to these common reasons are important action in protecting against porosity and making certain the high quality and strength of welded joints.Effects on Weld High Quality
The presence of porosity in a weld can substantially compromise the total quality and stability of the welded joint. Porosity within a weld produces gaps or dental caries that weaken the framework, making it more prone to cracking, rust, and mechanical failing. These voids serve as stress and anxiety concentrators, lowering the load-bearing capability of the weld and increasing the probability of early failing under used stress and anxiety. Furthermore, porosity can additionally function as possible sites for hydrogen entrapment, more worsening the destruction of the weld's mechanical buildings.In addition, porosity can prevent the efficiency of non-destructive testing (NDT) techniques, making it testing to find various other problems or gaps within the weld. This can result in significant safety and security problems, particularly in vital applications where the structural integrity of the bonded elements is vital.

Avoidance Techniques Overview
Offered the harmful effect of porosity on weld high quality, reliable avoidance techniques are critical to maintaining the structural stability of welded joints. Additionally, selecting the proper welding parameters, such as voltage, present, and travel speed, can aid minimize the risk of porosity development. By integrating these avoidance methods into welding techniques, the incident of porosity can be significantly lowered, leading to stronger and more trusted welded joints.Importance of Appropriate Shielding
Appropriate shielding in welding plays a critical function in preventing climatic contamination and making sure the integrity of bonded joints. Protecting like this gases, such as argon, helium, or a combination of both, are typically made use of to secure the weld swimming site web pool from responding with elements airborne like oxygen and nitrogen. When these responsive aspects come into call with the warm weld swimming pool, they can cause porosity, bring about weak welds with reduced mechanical residential or commercial properties.
Insufficient shielding can result in various defects like porosity, spatter, and oxidation, endangering the structural integrity of the welded joint. Adhering to correct protecting methods is vital to produce high-grade welds with minimal defects and make sure the more long life and integrity of the welded components.
Surveillance and Control Techniques
How can welders properly keep an eye on and control the welding procedure to make certain ideal results and stop problems like porosity? One trick technique is via making use of advanced tracking technologies. These can consist of real-time monitoring systems that give comments on criteria such as voltage, current, take a trip speed, and gas flow prices. By continuously checking these variables, welders can determine inconsistencies from the suitable problems and make immediate modifications to avoid porosity formation.
In addition, implementing proper training programs for welders is necessary for monitoring and controlling the welding process successfully. What is Porosity. Enlightening welders on the importance of maintaining consistent specifications, such as correct gas securing and travel speed, can help avoid porosity issues. Regular assessments and certifications can also guarantee that welders excel in tracking and regulating welding processes
Furthermore, the use of automated welding systems can improve tracking and control abilities. These systems can exactly regulate welding parameters, reducing the chance of human mistake and making certain constant weld high quality. By combining innovative surveillance innovations, training programs, and automated systems, welders can efficiently keep track of and regulate the welding procedure to reduce porosity defects and attain high-grade welds.
Final Thought
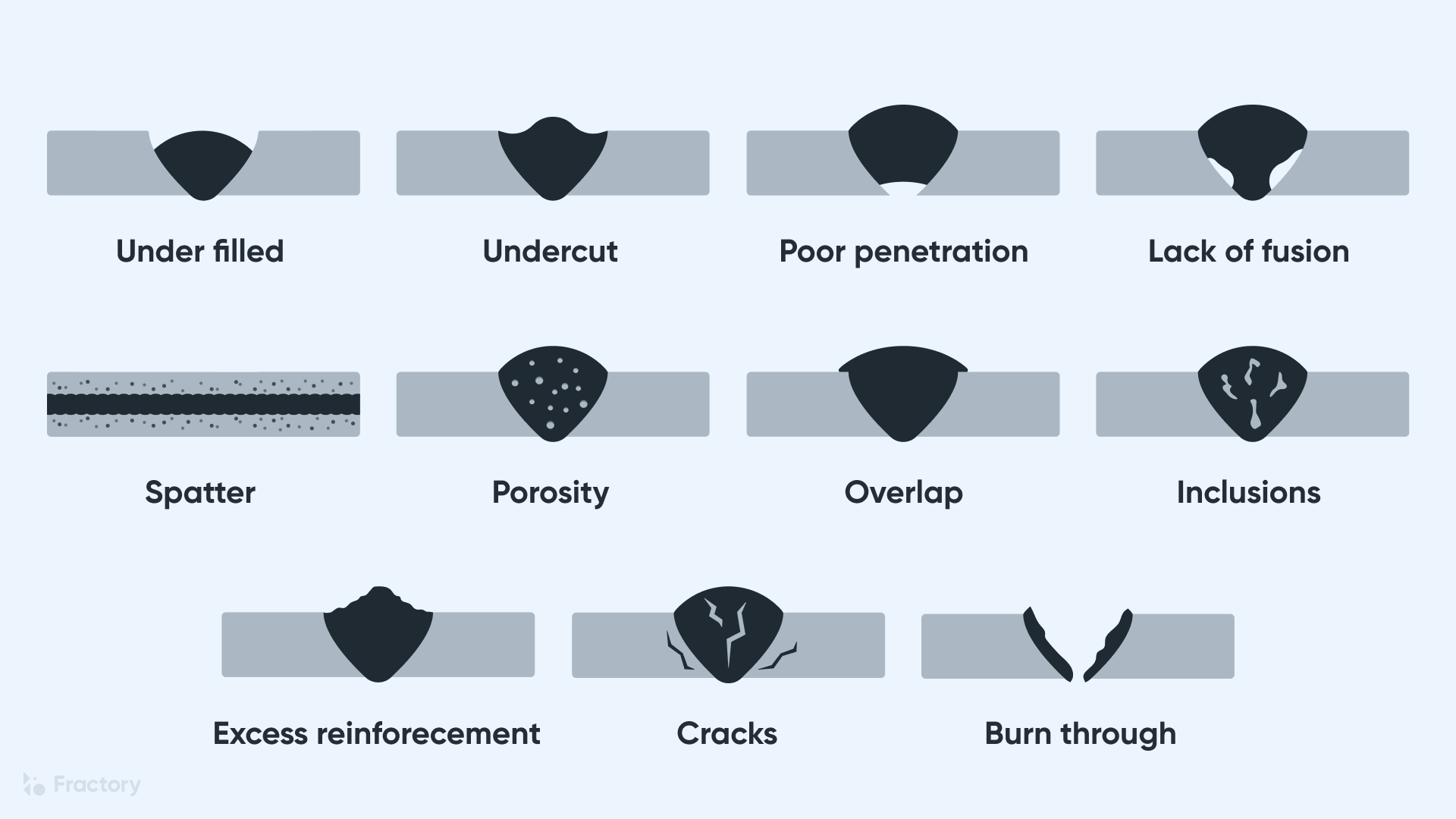
Report this wiki page